Start a Career That
Will Save the World
That’s a bold statement. And we believe it’s true. Because here, you’ll develop and expand our patented high-performance glass technologies that significantly reduce the energy used by buildings, creating the potential to affect climate change by dramatically lowering carbon emissions.
Start a Career That
Will Save the World
That’s a bold statement. And we believe it’s true. Because here, you’ll develop and expand our patented technologies that significantly reduce the energy used by buildings, creating the potential to affect climate change by dramatically lowering carbon emissions.
LuxWall was founded on our ability to See Beyond the global energy and environmental challenges of today.
Now, we’re looking for the people who will further develop and expand our products for global applications. We’re looking for you.
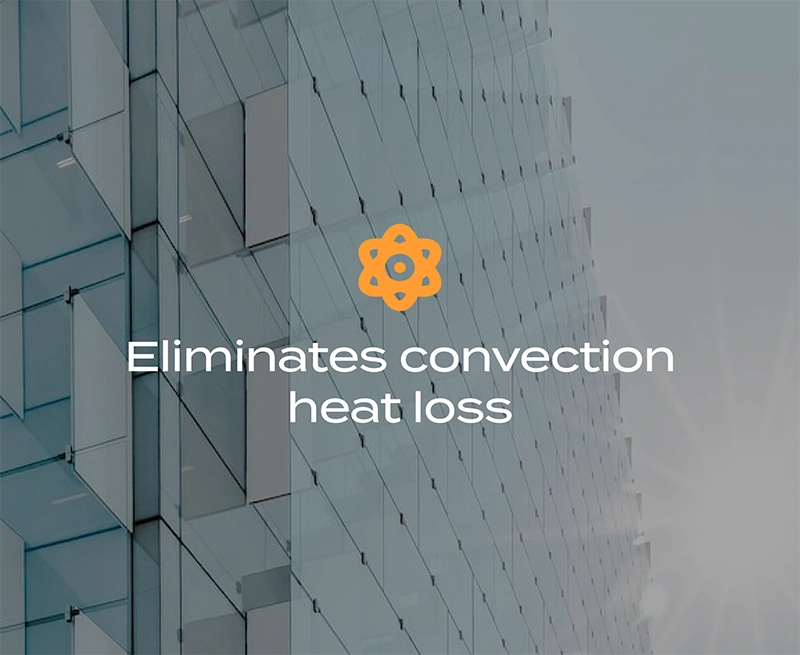
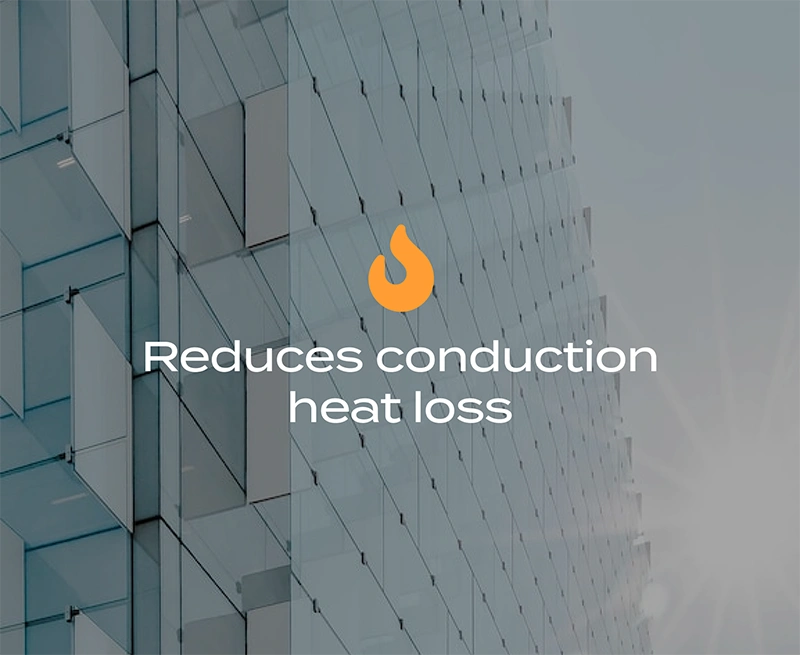
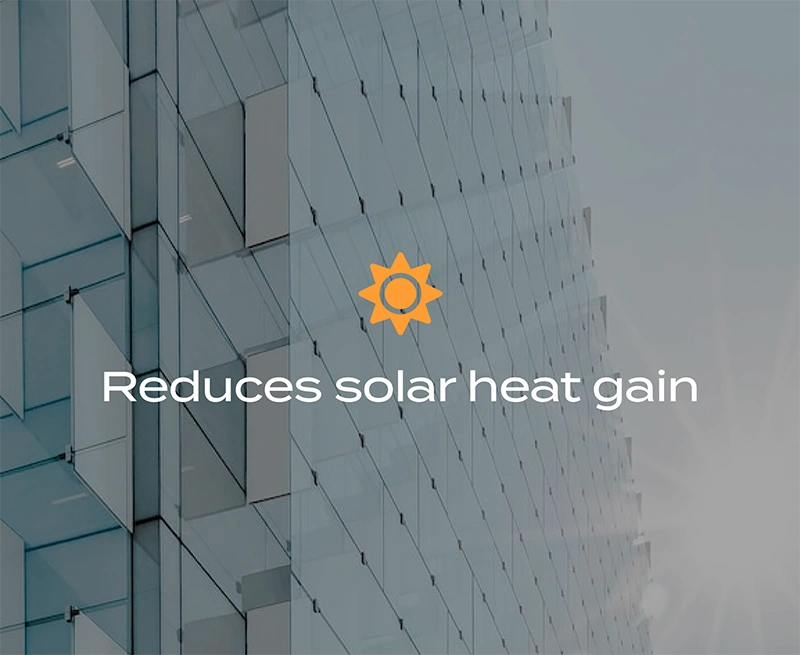
Saving the Planet Just Might be Your Destiny
Here, you’ll work hands-on with a first-to-market product in the industry – a patented new vacuum insulating glass technology that acts as transparent insulation for buildings. Our technological advancements in glass will accelerate us to net zero for buildings. And with mass adoption, LuxWall glass can reduce global carbon emissions by 14%.
Become an Essential Member
of a Meaningful Team
These are the values that guide us toward success every day. If this sounds inviting to you, let’s meet.
See Beyond
We see beyond what’s happened – and what’s coming. We see a portal to what’s possible, and a new instrument to dramatically reduce emissions. We see the power to connect humankind with a greater vision. We see a new era where all people across the planet are living more sustainable lives. Our purpose is clear. We are LuxWall. And we See Beyond.
Our Geniuses Love Their Jobs
Share in a thriving culture that celebrates individualism and diversity while fostering your personal achievement and success. Capitalize on the enthusiastic support of powerful venture capitalists, including Breakthrough Energy.
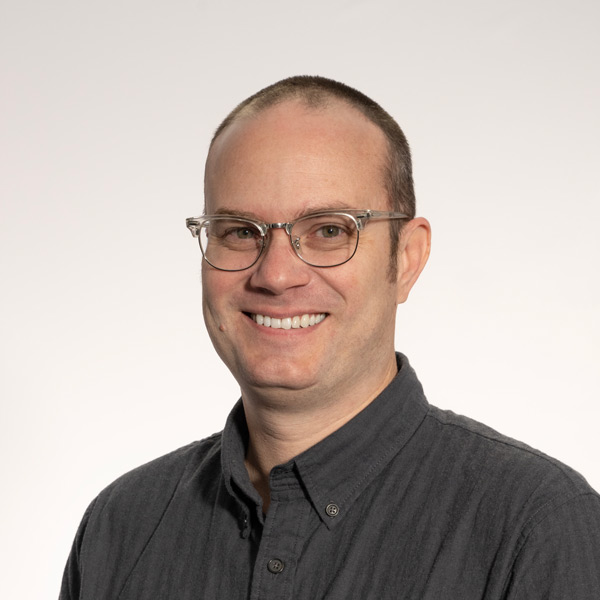
Christian Bischoff
Director of R&D
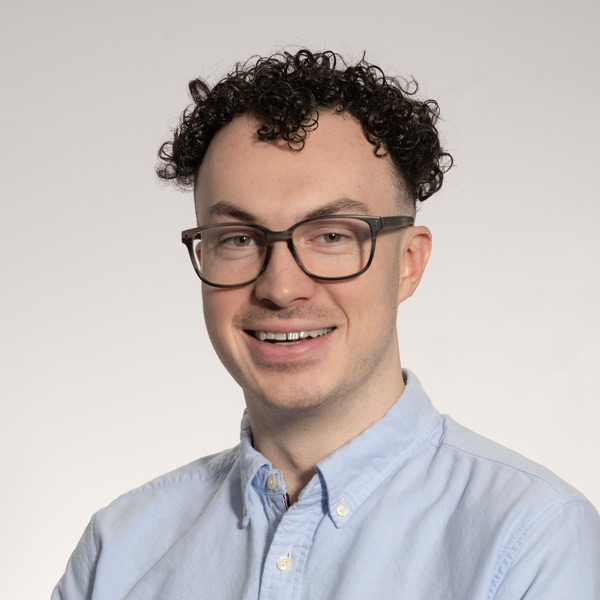
Riley Donahue
Ceramics Engineer
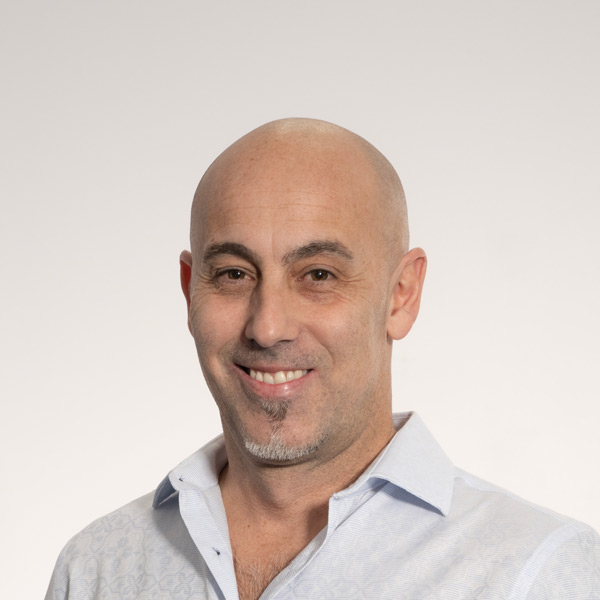
Maximo Frati
Senior Staff Engineer
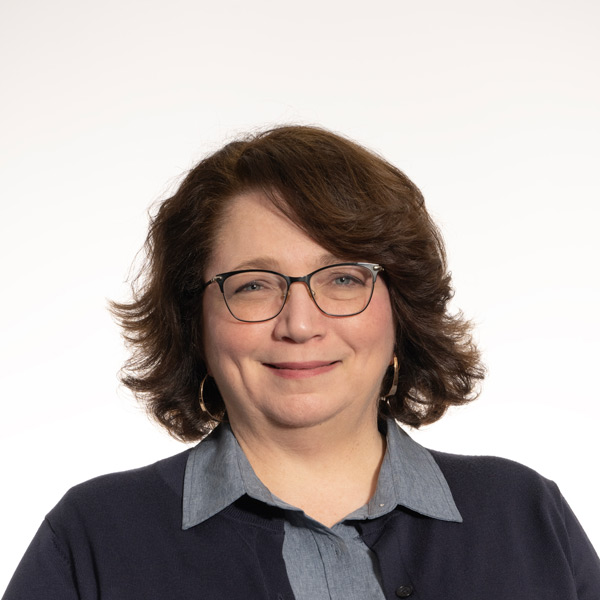
Lynda Navarre
Purchasing Manager
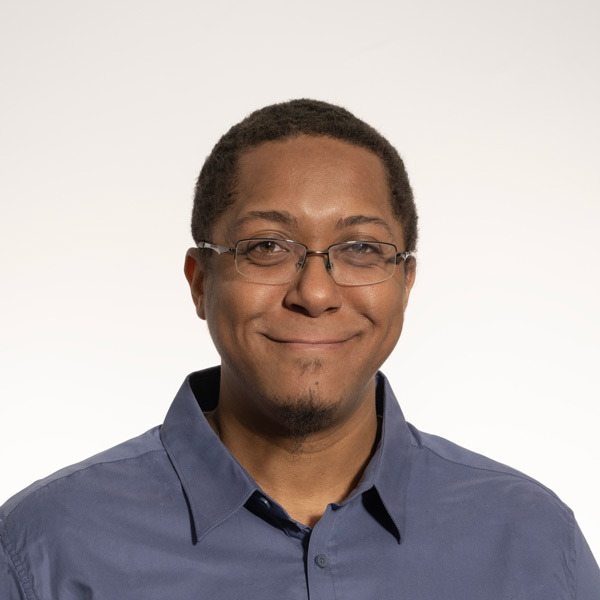
Shaun Jones
Test & Validation Engineer
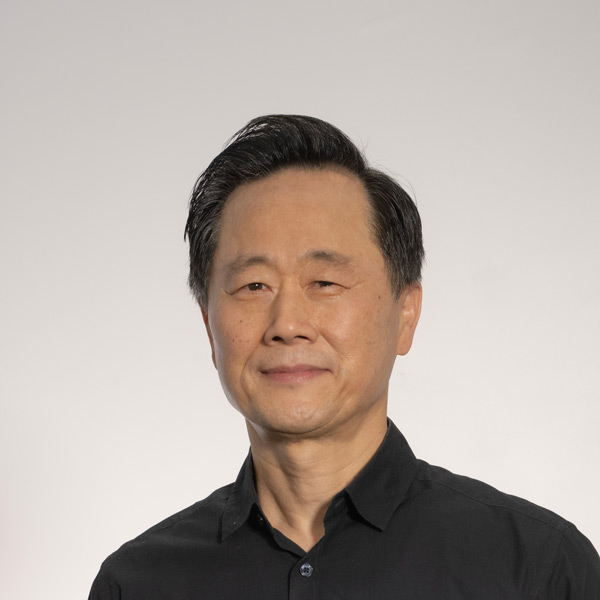
Jun Huh
Senior Staff Scientist
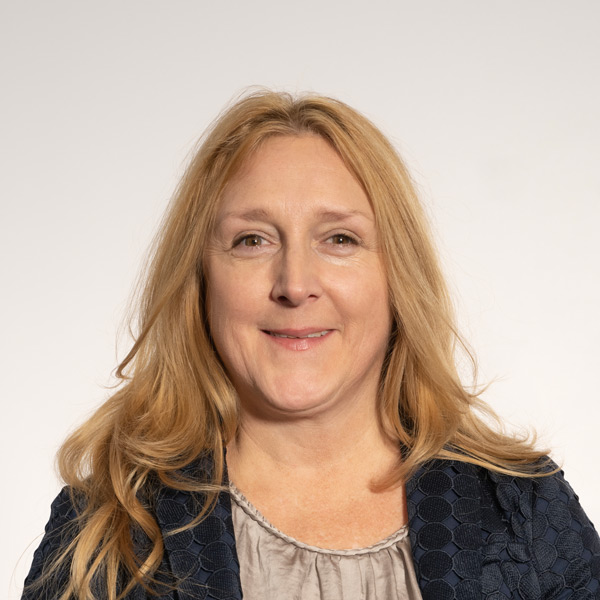
Jean Mayher
Vice President, Sustainability
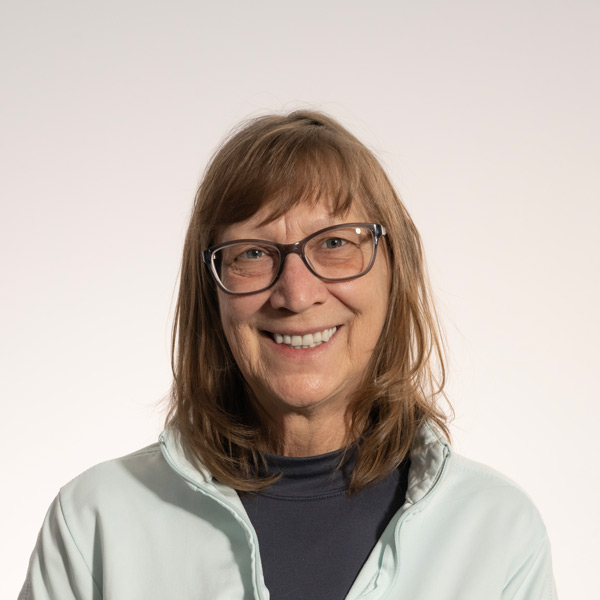
Ginger Pietka
Principal Engineer
Life-Changing Opportunities
80% of medical, dental and vision premiums covered for employees |
Health insurance coverage starts first day of the month following LuxWall date of hire if start date does not fall on the first of the month |
HMO, PPO or HSA medical plan and account options |
Employee Assistance Programs for employees provided by EmPower HR |
Twelve (12) company paid holidays and generous Paid Time Off policies |
80% of medical, dental and vision premiums covered for dependents |
12 weeks paid parental leave for the birthing parent and 4 weeks paid leave for the non-birthing parent |
Access to Dependent Care Account for Child Day Care or Adult Day Care |
Access to an Adoption Assistance Flexible Spending Account |
Access to Commuter Benefits Account with tax-free payments |
Employee stock options |
Finance and stock option education and tax advice provided by Carta |
Company-sponsored 401(k) through Schwab Financial Services with company match |
Employer-sponsored long-term disability and life insurance policies |
Company programs for personal and professional development |
Current Openings
LuxWall is focused on the product development, scaling, and commercializing of innovative glass products and solutions for the built environment. LuxWall’s transparent insulation technology, Enthermal, provides a step change in energy performance by significantly reducing convective, conductive, and radiative heat gain and heat loss in buildings. Acting as a transparent thermos bottle for buildings, LuxWall has the potential to reduce global carbon emissions by more than 0.5 gigaton per year with mass adoption. Enthermal will forever change the way buildings are designed and constructed for the future sustainability of our planet.
The Staff Engineer-Robotics will be responsible for developing, implementing, and optimizing manufacturing processes. They work closely with cross-functional teams to ensure the efficient production of high-quality products. Staff Engineer will involve leveraging advanced manufacturing technologies, continuous improvement methodologies, and innovative solutions to drive operational excellence. This position will be actively involved in the design and implementation of future manufacturing facilities and will support the company’s growth goals.
Position Responsibilities:
Robotics and Automation:
- Develop and optimize automated systems for clamp on/clamp off processes.
- Integrate automation and robotics into manufacturing processes to enhance productivity and quality.
- Evaluate and select appropriate technologies for manufacturing applications.
Fixture and Equipment Specification:
- Write equipment specifications and RFQs for manufacturing equipment.
- Design and specify fixtures, tools, and equipment required for manufacturing processes.
- Evaluate and select appropriate equipment and technologies for manufacturing.
- Ensure automated manual and assembly systems achieve critical targets, including output per hour, process yield, unscheduled downtime, MTTR, MTBF, the number of required operators, and other critical parameters per manufacturing planning and targets.
Supplier Sourcing:
- Identify and source suppliers for manufacturing equipment, materials, and services.
- Negotiate contracts and agreements with suppliers to ensure cost-effective procurement.
- Collaborate with suppliers to ensure equipment meets specifications and quality standards.
- Maintain strong relationships with suppliers to ensure timely delivery and quality compliance.
Equipment Installation and Commissioning:
- Oversee the installation and commissioning of manufacturing equipment and systems.
- Ensure equipment is installed and operational according to specifications and safety standards.
- Conduct equipment validation and performance testing to ensure optimal operation.
- Complete capability studies for new processes.
- Characterize heating and cooling processes using thermal measurement systems to ensure equipment is performing according to design criteria.
- Together with the operations team, ensure that all technicians are trained on the operation and safety of all equipment.
New Product and Facility Launch:
- Oversee the installation and commissioning of manufacturing equipment and systems.
- Ensure equipment is installed and operational according to specifications and safety standards.
- Conduct equipment validation and performance testing to ensure optimal operation.
- Complete capability studies for new processes.
- Characterize heating and cooling processes using thermal measurement systems to ensure equipment is performing according to design criteria.
- Together with the operations team, ensure that all technicians are trained on the operation and safety of all equipment.
Continuous Improvement:
- Identify opportunities for process improvements and cost reductions in manufacturing.
- Implement continuous improvement initiatives to enhance production efficiency and quality.
- Stay updated on industry trends and advancements in manufacturing technologies.
Position Requirements:
- Bachelor’s degree in Mechanical Engineering, Electrical Engineering or a related engineering discipline.
- 5+ years of demonstrated experience with new equipment design, builds, installation and debugging.
- 5+ years of proven experience in manufacturing engineering, with a focus on automation, part positioning, tolerances and GD&T.
- 5+ years of experience with design and operation of conveyance systems for substates at high temperatures.
- Deep understanding of manufacturing processes and workflow in a high-volume, highly automated operation.
- Experience with data acquisition and analysis from production equipment.
- Strong analytical and troubleshooting abilities.
- Experience writing and editing detailed equipment specifications.
- Deep understanding of manufacturing processes and workflow in a high-volume, highly automated operation.
- Experience with data acquisition and analysis from production equipment.
- Strong analytical and troubleshooting abilities.
- Ability to travel up to 40% within Michigan is required for this role.
- Excellent communication and collaboration skills to work with cross-functional teams.
- Proficient in Microsoft Project.
LuxWall, Inc. is an Equal Opportunity Employer. We do not discriminate based on race, color, religion, sex, sexual orientation, gender identity, national origin, disability, age, veteran status, or any other legally protected characteristics. All employment decisions are based on qualifications, merit, and business needs.
All applicants must complete and pass a drug screening and background check. LuxWall’s process is a 10-panel drug screen which includes marijuana.
LuxWall is focused on the product development, scaling, and commercializing of innovative glass products and solutions for the built environment. LuxWall’s transparent insulation technology, Enthermal, provides a step change in energy performance by significantly reducing convective, conductive, and radiative heat gain and heat loss in buildings. Acting as a transparent thermos bottle for buildings, LuxWall has the potential to reduce global carbon emissions by more than 0.5 gigaton per year with mass adoption. Enthermal will forever change the way buildings are designed and constructed for the future sustainability of our planet.
The Second Shift Process Operator will be responsible for operating and maintaining production machinery and equipment in a fast-paced manufacturing environment. You will be responsible for ensuring the efficient and safe production of high-quality products while adhering to established production standards and procedures.
** Second shift signing bonus of $ 1,000 upon completion of 30 days of employment.
** Shift premium available for second shift.
Position Responsibilities
- Understand and follow work instructions and control plans.
- Assist with other key tasks during changeovers.
- Quality checks with data input into the Quality System to keep the process running efficiently.
- Understanding trends on reliability and yield.
- Set-up and adjust equipment settings to meet production specifications and quality standards.
- Conduct regular inspections and quality checks to ensure products meet or exceed quality standards.
- Identify and resolve equipment malfunctions or operational issues in a timely manner, collaborating with Maintenance Technicians as needed.
- Perform routine maintenance tasks, such as cleaning, lubricating, and minor repairs, to keep equipment in optimal condition.
- Accurately record production data, equipment maintenance logs, and other relevant information.
- Adhere to all company safety policies and procedures.
- Identify opportunities for process improvement and efficiency enhancement, suggesting ideas and participating in implementation efforts.
- Participate in training programs to enhance skills and knowledge of equipment operation, safety procedures and production techniques.
Qualifications
- High school diploma or equivalent. Technical or vocational training in a manufacturing or a related field.
- Proven experience as a production operator or similar role in a manufacturing environment.
- Strong mechanical aptitude with the ability to operate and troubleshoot production machinery effectively.
- Ability to interpret technical manuals, diagrams, and instructions.
- Willingness to work in shifts and adapt to changing production schedules.
- Exceptional attention-to-detail and a high sense of urgency.
- Ability to stand frequently, walk, kneel, and bend.
- Physical strength to manage demands such as lifting heavy objects (50 lb. Minimum).
- Effective communication skills, both verbal and written, to interact with team members, contractors, and employees.
- Ability to work independently and prioritize tasks in a fast-paced environment.
Work Environment
- 100% Plant floor (PPE required)
-
Requires working in a fast-paced manufacturing environment with exposure to machinery, chemicals, and varying temperatures and noise levels.
- Constant communication with employees, peers and management
- Overtime as required
- Frequent requirement of handling heavy equipment (operation)
- Frequent need to give concentrated attention to surroundings
Physical Demands
- Standing and Walking: The role requires standing and walking for extended periods, up to 8-12 hours per shift, depending on production demands.
- Lifting and Carrying: Must be able to lift and carry objects weighing up to [weight, e.g., 50 lbs.] regularly throughout the shift. Occasional lifting of heavier items may be required with assistance.
- Bending, Stooping, and Crouching: Frequent bending, stooping, crouching, and reaching are necessary to perform tasks such as machine operation, product assembly, and maintenance.
- Pushing and Pulling: The position involves pushing and pulling carts, tools, and materials weighing up to [weight, e.g., 100 lbs.], either manually or using appropriate equipment.
- Manual Dexterity: The ability to use hands and fingers to handle, control, or feel objects, tools, or controls with precision is required for operating machinery, assembling products, and performing maintenance.
- Climbing: Occasional climbing of ladders or steps to access equipment or storage areas may be required.
- Vision and Hearing: Adequate vision is necessary to read and interpret technical documents, operate equipment, and inspect products for quality. Adequate hearing is required to communicate effectively in a noisy environment and to be aware of machinery sounds for safety.
- Repetitive Motions: This job may involve repetitive hand, wrist, and arm motions during tasks such as assembling parts, operating equipment, or packaging products.
- Environmental Conditions: The role may require working in varying temperatures, including cold storage areas or areas where heat from machinery is present. Exposure to dust, chemicals, fumes, and loud noises is common in manufacturing environments, and appropriate personal protective equipment (PPE) must be worn.
- Physical Stamina: The job requires maintaining high energy levels and physical stamina to keep up with the pace of production and meet performance targets
LuxWall, Inc. is an Equal Opportunity Employer. We do not discriminate based on race, color, religion, sex, sexual orientation, gender identity, national origin, disability, age, veteran status, or any other legally protected characteristics. All employment decisions are based on qualifications, merit, and business needs.
All applicants must complete and pass a drug screening and background check. LuxWall’s process is a 10-panel drug screen which includes marijuana.
LuxWall is focused on the product development, scaling and commercializing of innovative glass products and solutions for the built environment. LuxWall’s transparent insulation technology, Enthermal, provides a step change in energy performance by significantly reducing convective, conductive, and radiative heat gain and heat loss in buildings. Acting as a transparent thermos bottle for buildings, LuxWall has the potential to reduce global carbon emissions by more than 0.5 gigaton per year with mass adoption. Enthermal will forever change the way buildings are designed and constructed for the future sustainability of our planet.
The Sr. Controls Engineer will be responsible for designing, implementing, and maintaining Manufacturing Execution Systems (MES) and control systems to optimize production processes. Your expertise will be crucial in ensuring seamless integration between production equipment and enterprise systems, driving operational efficiency, and improving overall manufacturing performance.
Position Responsibilities:
- Develop, implement, and optimize control strategies for industrial automation systems.
- Ability to read, understand and modify electrical and network drawings. Experience with Rockwell Integrated Architecture Builder is preferred.
- Ability to select appropriate components to maximize system performance and control cost.
- Understanding of organized programming techniques including use of UDT’s and appropriate application of AOI’s.
- Design and program PLCs, HMIs, and SCADA systems. Design control systems to regulate the behavior of dynamic systems. This involves analyzing system requirements, developing mathematical models, and designing control algorithms to achieve desired performance objectives.
- Implement Control Algorithms: Once the control systems are designed, implement the control algorithms in software or hardware components, such as PLCs (Programmable Logic Controllers) or microcontrollers.
- Experience with Rockwell Studio5000 PLC and Ignition HMI platforms is preferred.
- Experience with various communication networks including TCP/IP, Profibus, Modbus TCP and Modbus RTU.
- Ability to use Bridges and Third-Party modules to integrate multiple communication protocols.
- Experience with Servo, VFD, and Direct Start Motors. CIP Motion experience is preferred.
- Experience with CIP Safety and Hardwired Safety applications.
- Experience Setting up and Interfacing with Barcode readers. Cognex and Keyence experience preferred.
- Integrate control systems with MES and other enterprise systems to enable real-time data acquisition and analysis.
- Implement and verify tracking systems to monitor progress of units through the production lines.
- Conduct system testing, validation, and troubleshooting to ensure functionality and performance. Fine-tune controller parameters to optimize system response and ensure stability and robustness.
- Monitoring System Performance: Continuously monitor the behavior of controlled processes, using feedback from sensors and other data sources. Assess system performance and adjust maintain optimal operation.
- Troubleshooting and Diagnostics: When control systems encounter issues or malfunctions, diagnose the problems and implement corrective actions to restore normal operation.
- Integration with Other Systems: Collaborate with other disciplines to integrate control systems into larger systems and processes. They ensure seamless communication and coordination between different components of the overall system.
- Documentation: Maintain detailed documentation of control system designs, configurations, and changes for reference and future troubleshooting.
- Upgrades and Enhancements: As technology evolves, upgrade control systems and incorporate new features or enhancements to improve system performance.
- Coordinate with cross-functional teams to ensure project milestones are met on time and within budget.</li
- Prepare and present technical documentation, reports, and project updates to stakeholders.
- Analyze production data to identify opportunities for process improvement and efficiency gains.
- Implement best practices and industry standards for MES and control systems.
- Stay current with emerging technologies and trends in manufacturing automation and MES solutions.
- Control engineers prioritize safety considerations in their designs and implementations, ensuring that control systems meet regulatory standards and safety requirements.
- Help build preventative and predictive maintenance requirements and plans for automation related equipment in manufacturing.
- Ensure programmed systems achieve critical targets including output per hour, process yield, unscheduled downtime, MTTR, MTBF, number of required operators and other critical parameters per manufacturing planning and targets.
- Ensure that all automation equipment is installed and operated in a safe manner and has appropriate engineering controls, where applicable, to ensure safe operation.
Position Requirements:
- Bachelor’s Degree in Electrical Engineering, Computer Science or a related engineering discipline.
- Highly proficient in PLC programming and communication, including Rockwell, Siemens, Yaskawa and Schneider.
- Extensive experience writing PLC code for new manufacturing processes.
- Extensive experience commissioning new equipment.
- Experience in MES and ERP software, such as Ignition and SAP.
- Experience with Barcode Readers preferred.
- Experience in glass fabrication preferred.
- Deep understanding of manufacturing processes and workflow.
- Experience with data acquisition and analysis from production equipment.
- Strong analytical and troubleshooting abilities
- Excellent communication and collaboration skills to work with cross-functional teams.
Work Environment:
- 100% Plant floor (PPE required)
- Requires working in a fast-paced manufacturing environment with exposure to machinery, chemicals, and varying temperatures and noise levels.
- Constant communication with employees, peers and management.
- Overtime as required.
- Frequent need to give concentrated attention to surroundings.
Physical Demands:
- Standing and Walking: The role requires standing and walking for extended periods, up to 8-12 hours per shift, depending on production demands.
- Lifting and Carrying: Must be able to lift and carry objects weighing up to [weight, e.g., 50 lbs.] regularly throughout the shift. Occasional lifting of heavier items may be required with assistance.
- Bending, Stooping, and Crouching: Frequent bending, stooping, crouching, and reaching are necessary to perform tasks such as machine operation, product assembly, and maintenance.
- Pushing and Pulling: The position involves pushing and pulling carts, tools, and materials weighing up to [weight, e.g., 100 lbs.], either manually or using appropriate equipment.
- Manual Dexterity: The ability to use hands and fingers to handle, control, or feel objects, tools, or controls with precision is required for operating machinery, assembling products, and performing maintenance.
- Climbing: Occasional climbing of ladders or steps to access equipment or storage areas may be required.
- Vision and Hearing: Adequate vision is necessary to read and interpret technical documents, operate equipment, and inspect products for quality. Adequate hearing is required to communicate effectively in a noisy environment and to be aware of machinery sounds for safety.
- Repetitive Motions: This job may involve repetitive hand, wrist, and arm motions during tasks such as assembling parts, operating equipment, or packaging products.
- Environmental Conditions: The role may require working in varying temperatures, including cold storage areas or areas where heat from machinery is present. Exposure to dust, chemicals, fumes, and loud noises is common in manufacturing environments, and appropriate personal protective equipment (PPE) must be worn.
- Physical Stamina: The job requires maintaining high energy levels and physical stamina to keep up with the pace of production and meet performance targets.
LuxWall, Inc. is an Equal Opportunity Employer. We do not discriminate based on race, color, religion, sex, sexual orientation, gender identity, national origin, disability, age, veteran status, or any other legally protected characteristics. All employment decisions are based on qualifications, merit, and business needs.
All applicants must complete and pass a drug screening and background check. LuxWall’s process is a 10-panel drug screen which includes marijuana.
LuxWall is focused on the product development, scaling, and commercializing of innovative glass products and solutions for the built environment. LuxWall’s transparent insulation technology, Enthermal™, provides a step change in energy performance by significantly reducing convective, conductive, and radiative heat gain and heat loss in buildings. Acting as a transparent thermos bottle for buildings, LuxWall has the potential to reduce global carbon emissions by more than 0.5 gigaton per year with mass adoption. Enthermal™ will forever change the way buildings are designed and constructed for the future sustainability of our planet.
The Second Shift Manufacturing Technician will be responsible for operating and maintaining production machinery and equipment in a fast-paced manufacturing environment. You will be responsible for ensuring the efficient and safe production of high-quality products while adhering to established production standards and procedures.
Position Responsibilities
- Ability to record data and recognize via SPC analysis whether a process is in or out of control.
- Quality checks with data input into the Quality System to keep the process running efficiently.
- Set-up and adjust equipment settings to meet production specifications and quality standards.
- Including navigation of HMI interface screens when powering up, troubleshooting, or operating automated equipment within the process.
- Conduct regular inspections and quality checks to ensure WIP & final products are conforming
- Identify and resolve equipment malfunctions or operational issues in a timely manner, collaborating with Maintenance Technicians, Process Engineers and Control Engineers.
- Perform routine maintenance tasks, such as cleaning, lubricating, and minor repairs, to keep equipment in optimal condition.
- Accurately record production data, equipment maintenance logs, and other relevant information.
- Understand and follow work instructions and control plans.
- Adhere to all company safety policies and procedures.
- Identify opportunities for process improvement and efficiency enhancement, suggesting ideas and participating in implementation efforts.
- Participate in training programs to enhance skills and knowledge of equipment operation, safety procedures and production techniques.
- Understanding trends on reliability and yield.
- Assist with other key tasks during changeovers.
- Possess the ability to learn in a high velocity environment to enable themselves to become flexible and fluent in the operation of multiple machine types. (“Quick Study” & “Multi-tasker”)
- Other duties as assigned.
Position Requirements:
- High school diploma or equivalent required. Technical or vocational training in a manufacturing or a related field is beneficial.
- Associate or Bachelor Degree in Electrical Engineering, Automation, Control Systems, or a related field, beneficial.
- 3-5 years working in a manufacturing environment required.
- Experience reading blueprints and maintaining strict product standards.
- Experience with operation of robotics and high-precision gantry systems.
- Experience with machine vision systems.
- Strict adherence to Standard Work Instructions with a focus on quality control.
- Proven experience as a production operator or similar role in a manufacturing environment.
- Strong mechanical and technical aptitude with the ability to operate and troubleshoot production machinery effectively.
- Ability to interpret technical manuals, diagrams, and instructions.
- Experience operating equipment via an HMI.
- Willingness to work in shifts and adapt to changing production schedules.
- Exceptional attention-to-detail and a high sense of urgency.
- Ability to stand frequently, walk, kneel, and bend.
- Physical strength to manage demands such as lifting heavy objects (50 lb. Minimum).
- Effective communication skills, both verbal and written, to interact with team members, contractors, and employees.
- Ability to work independently and prioritize tasks in a fast-paced environment.
- Glass manufacturing experience is a plus.
- Proficiency in forklift operation is a plus.
- **Second shift signing bonus of $ 1,000 upon completion of 30 days of employment**
- **Shift premium available for second shift.**
All applicants must complete and pass a drug screening and background check. LuxWall’s process is a 10-panel drug screen, which includes marijuana.
LuxWall is focused on the product development, scaling, and commercializing of innovative glass products and solutions for the built environment. LuxWall’s transparent insulation technology, Enthermal™, provides a step change in energy performance by significantly reducing convective, conductive, and radiative heat gain and heat loss in buildings. Acting as a transparent thermos bottle for buildings, LuxWall has the potential to reduce global carbon emissions by more than 0.5 gigaton per year with mass adoption. Enthermal™ will forever change the way buildings are designed and constructed for the future sustainability of our planet.
The Staff Engineer-Glass Tempering will be responsible for specifying, designing, installing and optimizing manufacturing tools. They will ensure that assigned tools are designed and built on time and to the performance required to support the company’s technology and business goals. This position will be actively involved in design and implementation of future manufacturing facilities and will support the company’s growth goals.
Position Responsibilities:
- Lead by example to drive a safety-first culture in all aspects of the workplace.
- Write equipment specifications and RFQs for new and used equipment.
- Evaluating existing processes and procedures to identify areas that need optimization.
- Present proposed equipment designs at scaling design reviews to solicit feedback from scaling team and leadership team.
- Collaborate with equipment suppliers and integrators to ensure equipment meets performance and cost requirements.
- Collaborate with the cross functional team and supply chain to issue POs for equipment.
- Take the lead with mechanical and electrical contractors to install the necessary equipment and infrastructure for new manufacturing tools.
- Ensure that all equipment is installed and operated in a safe manner and has appropriate engineering controls, where applicable, to ensure safe operation.
- Specify, design, install and conduct FAT/SAT for new equipment builds.
- Together with the operations team, ensure that all technicians are trained on the operation and safety of all equipment.
- Collaborate with the high volume manufacturing team to launch all manufacturing tools.
- Ability to read, understand and modify electrical and network drawings. Experience with Rockwell Integrated Architecture Builder is preferred.
- Participate in PFMEA, Control Plan and SOP generation associated with launches.
- Take full ownership of glass tempering and associated QC equipment from specification through production ramp.
- Characterize heating and cooling processes using thermal measurement systems to ensure equipment is performing according to design criteria.
- Train factory operations personnel to conduct thermal profiling of heating equipment to ensure compliance with design performance.
- Complete capability studies for new processes.
- Coordinate with cross-functional teams to ensure project milestones are met on time and within budget.
- Prepare and present technical documentation, reports, and project updates to stakeholders.
- Analyze production data to identify opportunities for process improvement and efficiency gains.
- Lead and direct the rollout of equipment modifications and upgrades in all Luxwall production facilities. Maintain a matrix of equipment revs to track facility-to-facility tool differences.
- Help build preventative and predictive maintenance requirements.
- Ensure thermal systems achieve critical targets including output per hour, process yield, unscheduled downtime, MTTR, MTBF, number of required operators and other critical parameters per manufacturing planning and targets.
Position Requirements:
- Bachelor’s Degree in Mechanical Engineering, Electrical Engineering or a related engineering discipline.
- Demonstrated experience with new equipment design, builds, installation and debugging.
- Extensive knowledge of heat transfer mechanisms.
- Extensive experience with commissioning and operation of glass tempering furnaces, including optimizing the operation for glass flatness and stress profile.
- Extensive experience with tempered glass QC procedures and equipment used to measure glass flatness.
- Demonstrated experience tempering glass with low emissivity coatings.
- Experience with design and operation of conveyance systems for substates at high temperatures.
- Thermal modeling experience a plus.
- Extensive experience commissioning new equipment.
- Experience in Ignition software.
- Deep understanding of manufacturing processes and workflow in a high-volume, highly automated operation.
- Experience with data acquisition and analysis from production equipment.
- Experience writing and editing detailed equipment specifications.
- Strong analytical and troubleshooting abilities.
- Excellent communication and collaboration skills to work with cross-functional teams.
- Proficient in Microsoft Project.
LuxWall, Inc. is an Equal Opportunity Employer. We do not discriminate based on race, color, religion, sex, sexual orientation, gender identity, national origin, disability, age, veteran status, or any other legally protected characteristics. All employment decisions are based on qualifications, merit, and business needs.
All applicants must complete and pass a drug screening and background check. LuxWall’s process is a 10-panel drug screen which includes marijuana.
LuxWall is focused on the product development, scaling, and commercializing of innovative glass products and solutions for the built environment. LuxWall’s transparent insulation technology, Enthermal, provides a step change in energy performance by significantly reducing convective, conductive, and radiative heat gain and heat loss in buildings. Acting as a transparent thermos bottle for buildings, LuxWall has the potential to reduce global carbon emissions by more than 0.5 gigaton per year with mass adoption. Enthermal will forever change the way buildings are designed and constructed for the future sustainability of our planet.
The Process Engineer will play a critical role in analyzing, designing, and optimizing production processes to enhance efficiency, reduce waste, and improve product quality to LuxWall’s R&D and Factory Manufacturing lines. This position requires a strong analytical mindset, attention to detail, and a passion for problem-solving.
Position Requirements
- Evaluate current manufacturing processes to identify areas for improvement and optimization.
- Develop and implement new manufacturing processes and techniques to enhance productivity and quality.
- Lead continuous improvement initiatives using methodologies such as Lean, Six Sigma, and Kaizen.
- Collect and analyze process data to identify trends, variances, and opportunities for improvement.
- Ensure that all processes comply with quality standards and regulations.
- Identify and implement cost-saving measures without compromising product quality.
- Lead mechanical and electrical contractors to install necessary equipment in a safe manner and have appropriate engineering controls to ensure safe operation.
- Work closely with cross-functional teams, including production, quality, and maintenance, to ensure seamless process integration.
- Maintain detailed documentation of process changes, improvements, work instructions, and standard operating procedures (SOPs) to support ISO and IATF.
- Provide training and support to production staff on new processes and improvements.
Position Qualifications:
- Bachelor’s degree in Chemical Engineering, Mechanical Engineering, Industrial Engineering, Physical Science or Engineering Technology Degree.
- Minimum of 5 years of experience in process engineering or a related role in a manufacturing environment.
- Proficiency in process simulation software and statistical analysis tools. Experience with 2D or 3D design software, a plus. Ability to read and interpret engineering MEP drawings. Extensive experience formulating and managing project schedules using WBS and Gantt charts.
- Knowledge of building codes, laws and regulations.
- Strong analytical and problem-solving skills with a data-driven approach.
- Experience in managing process improvement projects from inception to completion.
- In-depth knowledge of quality control principles and practices.
- Excellent verbal and written communication skills, with the ability to convey technical information clearly.
- Six Sigma certification (Green Belt or Black Belt) is highly desirable.
- High level of attention to detail and accuracy in all tasks.
- Ability to work effectively in a team-oriented environment and collaborate with cross-functional teams.
- Experience working with glass, coatings, fabricated glass and glass systems, a plus.
Work Environment
- 75% Plant floor (PPE required)
-
Requires working in a fast-paced manufacturing environment with exposure to machinery, chemicals, and varying temperatures and noise levels.
- Constant communication with employees, peers and management
- Overtime as required
- Frequent requirement of handling heavy equipment (operation)
- Frequent need to give concentrated attention to surroundings
Physical Demands
- Standing and Walking: The role requires standing and walking for extended periods, up to 8-12 hours per shift, depending on production demands.
- Lifting and Carrying: Must be able to lift and carry objects weighing up to [weight, e.g., 50 lbs.] regularly throughout the shift. Occasional lifting of heavier items may be required with assistance.
- Bending, Stooping, and Crouching: Frequent bending, stooping, crouching, and reaching are necessary to perform tasks such as machine operation, product assembly, and maintenance.
- Pushing and Pulling: The position involves pushing and pulling carts, tools, and materials weighing up to [weight, e.g., 100 lbs.], either manually or using appropriate equipment.
- Manual Dexterity: The ability to use hands and fingers to handle, control, or feel objects, tools, or controls with precision is required for operating machinery, assembling products, and performing maintenance.
- Climbing: Occasional climbing of ladders or steps to access equipment or storage areas may be required.
- Vision and Hearing: Adequate vision is necessary to read and interpret technical documents, operate equipment, and inspect products for quality. Adequate hearing is required to communicate effectively in a noisy environment and to be aware of machinery sounds for safety.
- Repetitive Motions: This job may involve repetitive hand, wrist, and arm motions during tasks such as assembling parts, operating equipment, or packaging products.
- Environmental Conditions: The role may require working in varying temperatures, including cold storage areas or areas where heat from machinery is present. Exposure to dust, chemicals, fumes, and loud noises is common in manufacturing environments, and appropriate personal protective equipment (PPE) must be worn.
- Physical Stamina: The job requires maintaining high energy levels and physical stamina to keep up with the pace of production and meet performance targets
LuxWall, Inc. is an Equal Opportunity Employer. We do not discriminate based on race, color, religion, sex, sexual orientation, gender identity, national origin, disability, age, veteran status, or any other legally protected characteristics. All employment decisions are based on qualifications, merit, and business needs.
All applicants must complete and pass a drug screening and background check. LuxWall’s process is a 10-panel drug screen which includes marijuana.